반응형
개요
- 기초파일은 연약지반에 건축물을 축조할 때 기초의 지내력을 증대시키기 위해 지중에 파일을 박거나 구축하는 공사로 주로 토목구조물 기초에 사용된다.
- 파일 작업시에는 인양 중 파일 낙하, 이동 시 항타기 전도, 파일 천공 시 흙더미 낙하에 의한 재해가 주로 발생된다.
단위작업 분류 및 순서
- 장비반입 및 조립
- 파일반입 및 적재
- 파일천공 및 근입
- 파일항타 작업
- 두부정리 작업
- 장비헤체 및 반출
1. 장비반입 및 조립 작업
분류 | 유해위험요인 | 감소대책 |
인적 요인 | 지게차 운전원의 운전 미숙으로 하역중 충돌 | 지게차 운전원의 자격여부를 사전에 확인하고 작업실시 |
작업자가 인양화물에 접촉위험 | 신호수 배치 및 신호 확인 | |
장비조립시 손, 손가락 끼임사고 | 핀 구멍에 절대로 손, 손가락을 넣지 않는다 | |
기계적 요인 | 장비배치 이동시 항타기 전도 | 항타기 이동시 철판 깔고 이동 |
장비조립 작업대 미설치 상태에서 고소작업시 추락 | 장비조립시 이동식 비계 설치 후 작업 | |
기계 투입 작업시 인양화물과 물체사이에 끼어서 부상위험 | 작업자는 인양화물에서 멀리 떨어져 인양화물과 물체 사이에 들어가지 못하도록 조치 | |
인양기구의 파손으로 인한 기계 낙하위험 | 인양화물에 적합한 인양기구를 선정하고 작업개시 전 점검 실시 | |
슬링밸트, 와이어로프 파단으로 인한 기계 낙하위험 | 작업개시 전 슬링밸트, 와이어로프 점검 | |
장비 반입 하역 작업시 장비 전도 | 장비의 하역위치 선정 철저 및 하역 작업계획 수립 후 작업 실시 | |
지게차 후면에 경광등 미설치로 후진하는 지게차에 충돌 | 지게차 후면부에는 경광등 설치하여 주변 근로자에게 경고조치 | |
조립작업시 협착 | 조립작업시 신호체계 확립 및 공구 사용하여 조정 | |
전기적 요인 | 불량 공도구 사용으로 인한 감전 | 사용전 기계의 점검, 외함접지 설치 상태 확인 및 충전부위 절연조치 실시 |
가설전선 피복 노출에 의한 감전 | 가설전선은 가공으로 배선하여 피복이 손상되지 않도록 하고 손상된 전선은 절연처리 하고 작업 | |
작업특성 요인 | 중량의 장비 부재를 인양 설치 작업시 인양장비의 전도, 인양 줄걸이의 파단에 의한 낙하 | 중량물 취급작업계획 및 차량계 건설기계의 작업계획을 수립 작성/검토/승인 후 작업 실시 |
작업환경 요인 | 작업장 주변 고압선로 접촉 사고 | 장비조립장 등 주변에 고압선로 등 지장물 현황파악 |
2. 파일반입 및 적재 작업
분류 | 유해위험요인 | 감소대책 |
인적 요인 | 자재운반차량에 줄걸이 작업을 위해 근로자 파일위로 이동하면서 작업중 미끄러져 추락 | 줄걸이 작업자 2인 배치 배관 양단에 사다리 등을 놓고 줄걸이 작업 실시 |
자재 적치중 손등,발등 협착 | 자재 적재작업시 평탄한 지역에 구름방지용 쐐기목을 고이고 관하부에 손과 발등 신체가 놓이지 않게 작업 | |
기계적 요인 | 경사지에서 지게차로 배관자재를 하역중 낙하 | 배관자재를 지게차 등으로 하역시 구름방지, 미끄러짐 방지조치를 하고 균형을 유지하여 하역 |
지게차의 용량을 초과하여 작업중 전도, 자재낙하 | 지게차 용량을 확인하여 선정 | |
자재 적치장 구역구분 미흡으로 인한 사고 | 자재 적재구역을 구분하고 관계자 외 출입을 금지 | |
인양 와이어로프가 자재 인양 중 끊기면서 낙하 | 인양로프는 손상이 없고 견고한 것 사용/사전점검 | |
자재 인양작업중 자재가 크게 흔들리면서 충돌 | 유도로프 등을 사용하여 자재가 요동치는 것 방지 | |
크레인 줄걸이 불량, 권과방지장치 등 이상으로 사고 | 작업전 크레인 안전점검, 줄걸이 상태 안전점검 실시 | |
자재운반차량에 줄걸이 작업을 위해 근로자 파일위로 이동하면서 작업중 미끄러져 추락 | 줄걸이 작업자 2인 배치 배관 양단에 사다리 등을 놓고 줄걸이 작업 실시 | |
이동식 크레인으로 자재 하역중 크레인 전도 | 아웃트리거는 견고하고 평탄한 지반에 거치, 붐의 각도는 인양하중 조견표에 따라 적정하게 유지 | |
전기적 요인 | 가설전선 피복 노출에 의한 감전 | 가설전선은 가공으로 배선하여 피복이 손상되지 않도록 하고 손상된 전선은 절연처리 하고 작업 |
재료적 요인 | 재료가 중량물이고 구르기 쉬운 자재로 취급 및 적재 불량으로 인한 협착 | 자재적재 작업시 받침목, 구름방지용 쐐기 등을 사전에 준비하여 작업시 사용 |
작업특성 요인 | 중량물 취급에 따른 안전작업 미흡으로 인한 사고 | 중량물 취급 및 차량계 건설기계 작업계획서를 작성/검토/승인 후 작업 실시 |
작업환경 요인 | 주변에 고압선 등에 크레인 붐대가 접촉되는 사고 | 자재 하역 및 적재 작업시 적재장은 지장물이 없는 곳으로 하고, 지장물 주변 작업시 신호수 배치하여 작업 |
3. 파일천공 및 근입 작업
분류 | 유해위험요인 | 감소대책 |
인적 요인 | 부적절한 장비 및 운전원 운전미숙으로 충돌, 협착 | 장비관련 법적서류 및 운전원 자격서류 징수 |
항타기 운전원과 조립공과의 신호 불일치로 낙하, 협착 | 신호방법 사전 협의 및 신호중계 유도원 배치 | |
기계적 요인 | 천공작업 및 이동중 지반침하로 장비 전도 | 천공기 하부 지반 침하방지 조치(철판 25mm이상) |
천공 작업중 스크류 상부의 흙덩어리가 낙하 | 덮개 설치, 항타기 운전원 유자격자 채용 및 오작동 방지 주지 교육 | |
로드 교체 작업시 추락위험 및 천공 홀에 근로자 추락 | 안전대 체결 등 안전보호구 착용 및 추락방지용 개구부 덮개 및 위험표지 부착 | |
천공기 하부 지반 침하방지조치 미실시로 전도 및 천공기 붐대와 리더의 연결부가 파단 리더낙하 | 침목, 철판 등으로 침하방지 조치 및 작업전 붐대와 리더의 연결부 및 용접부 체결 상태 점검 | |
전기적 요인 | 불량 공도구 사용으로 인한 감전 | 사용전 기계의 점검, 외함접지 설치 상태 확인 및 충전부위 절연조치 실시 |
가설전선 피복 노출에 의한 감전 | 가설전선은 가공으로 배선하여 피복이 손상되지 않도록 하고 손상된 전선은 절연처리 하고 작업 | |
작업특성 요인 | 도심지 천공작업에 따른 소음, 비산먼지 등에 의한 사고 | 도심지 천공에 적합한 장비 선정 및 소음, 진동, 비산먼지 저감장치 설치 |
중량의 장비 부재를 인양 설치 작업시 인양장비의 전도, 인양 줄걸이의 파단에 의한 낙하 | 중량물 취급작업계획 및 차량계 건설기계의 작업계획을 수립 작성/검토/승인 후 작업 실시 | |
작업환경 요인 | 작업시 지상, 지하의 고압선로 접촉 등 지장물 파손에 의한 사고 | 작업시 지장물 조사 철저 및 안전조치 후 작업 실시 |
4. 파일항타 작업
분류 | 유해위험요인 | 감소대책 |
인적 요인 | 운반차량 적재함에 승/하강 중 뛰어내리는 등 불안전한 행동사고 | 차량적재함 승/하강시 뛰어내리지 않도록 교육 |
기계적 요인 | 파일항타 중 햄머와이어 파단으로 낙하 | 와이어의 손상유무를 수시로 점검 조치 |
항타기 붐대와 리더의 연결부가 탈락되어 리더낙하 | 항타기 붐대와 리더의 연결부 및 용접부 체결 | |
항타기 햄머 인상 상태에서 하부 점검 중 햄머 낙하 | 햄머를 인상시켜 놓은 상태에서 하부 작업금지, 햄머를 이동시켜 놓은 상태에서 파일상태 점검실시 | |
연약지반 또는 장비 불안전 셋팅으로 장비 전도 | 연약지반에서 장비작업에 다른 전도방지를 위한 깔판 설치(작업중,, 이동시) | |
항타 작업중 항타기 붐대가 부러지면서 항타기 리더 전도 | 항타기 붐대 견고성,기계장치의 이상유무 등을 사전 점검 후 작업시행 | |
강관파일 세우기 작업중 와이어로프 탈락으로 전도, 협착 | 강관파일 세우기 작업시 와이어로프의 견고한 체결 및 확인 | |
전기적 요인 | 불량공도구 사용으로 인한 감전 | 사용전 기계의 외함접지 설치 상태 확인 및 충전부위 절연조치 실시 |
가설전선 피복 노출에 의한 감전 | 가설전선은 가공으로 배선하여 피복이 손상되지 않도록 하고 손상된 전선은 절연처리 하고 작업 | |
작업특성 요인 | 중량의 장비 부재를 인양 설치 작업시 인양장비의 전도, 인양 줄걸이의 파단에 의한 낙하 | 중량물 취급작업계획 및 차량계 건설기계의 작업계획을 수립 작성/검토/승인 후 작업 실시 |
작업환경 요인 | 지상에 적치된 자재 인력으로 운반 중 자세불량, 무리한 힘 요통 | 중량물 인력운반 교육 실시 스트레칭 교육실시 |
5. 두부정리 작업
분류 | 유해위험요인 | 감소대책 |
인적 요인 | 보안경 미착용 상태에서 고압가스절단기 작업중 비산물 사고 | 산소 절단 작업시 보안경 착용 |
장비작업자 운전 미숙으로 인한 주변 작업자 충돌, 협착 | 장비 작업자 사전 자격 확인 철저 | |
기계적 요인 | 파일절단면(산소절단)을 그라인딩시 그라인더 날에 접촉 상해 | 그라인더 날 접촉부에 방호덮개 설치 |
파일 컷팅 작업중 (산소절단) 넘어가는 파일에 충돌협착 | 파일 컷팅 작업자 안전구역 위치 선정 및 개인보호구 착용 철저 | |
두부정리후 파일 개구부로 추락 | 두부정리후 강관 파일 상단부에 추락방지용 덮개 설치하여 개구부 차단 조치 | |
강관 파일 산소절단시 불티가 눈에 튀어 상해 | 산소 절단 작업시 보안경 착용 | |
고속절단기로 파일 두부 정리시 날에 접촉 베임 | 날접촉 방지 장치 설치 및 작업시 베임에 주의 | |
굴삭기 버켓 탈락으로 하부근로자 협착 | 굴삭기 버켓 탈락 안전핀 체결 확인 | |
굴삭기 작업반경내 작업중 회전하는 굴삭기에 충돌, 협착 | 굴삭기 작업반경내 접근 금지 및 작업중 신호수 배치 | |
전기적 요인 | 불량 공도구 사용으로 인한 감전 | 사용전 기계의 외함접지 설치 상태 확인 및 충전부위 절연조치 실시 |
가설전선 피복 노출에 의한 감전 | 가설전선은 가공으로 배선하여 피복이 손상되지 않도록 하고 손상된 전선은 절연처리 하고 작업 | |
작업특성 요인 | 장비와 인력을 이용하여 파일 컷팅시 장비로 컷팅한 파일이 작업자에거 전도 | 두부정리시 장비와 인력 작업의 일정한 거리를 두고 작업 |
작업환경 요인 | 파일컷팅 그라인더 작업시 비산칩이 눈과 호흡기로 들어감 | 파일컷팅시 보안경, 방진마스크 착용 철저 |
6. 장비해체 및 반출 작업
분류 | 유해위험요인 | 감소대책 |
인적 요인 | 장비 상부 해체 시 추락 | 고소부위 장비 해체시 안전대 착용 |
장비 및 공도구 낙하,협착 | 조립 위한 장비인양시 낙하 및 협착예방, 접근통제 | |
기계적 요인 | 장비후진 중 근로자와 충돌 | 후진경보장치 및 후방카메라 설치 |
장비 전도사고 | 장비 완전 해체후 깔판 제거 | |
자재 운반차량 후진 중 근로자와 충돌 | 차량계 하역운반기계 사용시 유도자를 배치하여 유도 | |
해체한 장비 부재 인양 중 로프가 끊어져 낙하 | 인양줄걸이 사전 점검 철저 | |
전기적 요인 | 불량 공도구 사용으로 인한 감전 | 사용전 기계의 외함접지 설치 상태 확인 및 충전부위 절연조치 실시 |
가설전선 피복 노출 감전 | 가설전선이 훼손되지 않도록 배선하고 수시로 확인 | |
작업특성 요인 | 장비해체 작업 순서 미준수로 인한 자체 반력 등에 의한 튕김에 의한 사고 | 장비의 해체 작업전 해체순서 및 방법에 대해 교육 후 실시 |
기초파일(강관) 작업 재해 사례
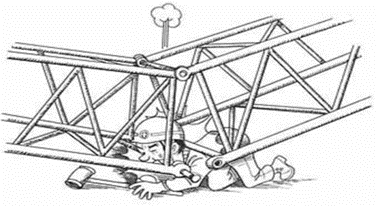
- 재해개요
- 항타기 붐을 해체하기 위해 붐을 수평으로 고정시킨 후 붐하부에서 연결핀을 해체하던중 붐이 꺾이면서 협착, 병원으로 후송중 사망한 재해
- 재해원인
- 크레인 붐 해체방법 불량
- 안전대책
- 항타기 크레인 붐을 해체하기 위해서는 크레인의 권상용 와이어로프를 중간 붐 상부고리에 걸고 붐 끝단에는 받침목을 고정후 하부 PIN을 제거해야 함
- 형태
- 협착
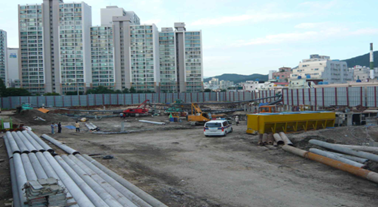
- 재해개요
- 지반이 침하되면서 넘어져 인근에 작업중이던 이동식크레인과 충돌하고 넘어진 이동식크레인 붐이 다시 1호 항타기와 연쇄적으로 충돌 후 굴삭기를 덮쳐 굴삭기 운전원은 운전석에서 협착 사망하고 1호 항타기 운전원은 운전석에서 탈출 중 부상당한 재해
- 재해원인
- 작업계획서 미작성
- 지반보강 미실시
- 안전대책
- 차량계 건설기계 사용 작업시 사전에 작업장소의 지반상태 등을 조사하고 그 결과를 고려하여 운행경로, 작업방법 등에 대한 작업계획 작성 후 그 계획에 따라 작업
- 차량계 건설기계가 넘어지는 등의 위험이 우려될 때에는 지반보강 등 부등침하방지, 도로 폭 유지 등 필요한 조치를 하여야 함.
- 형태
- 전도
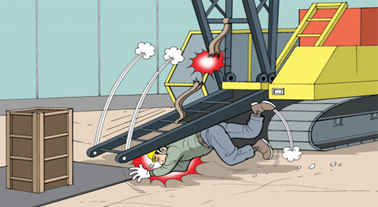
- 재해개요
- 항타기리더와 붐 사이 바닥에 깔려 있는 이동전선을 정리 하던 중, 항타기 리더 고정용 지지대를 붐에 결속하여 지탱하던 섬유로프가 파단 되면서 지지대가 피재자를 가격ㆍ사망한 재해임
- 재해원인
- 리더연결지지대 결속 줄걸이 확인 미흡
- 지지력 미확보된 슬링벨트 사용
- 안전대책
- 항타기 조립작업시에는 사전에 크롤러 크레인과 항타기 리더의 연결 지지대를 결속할 줄걸이의 상태를 확인
- 지지력이 확보된 충분한 강도의 자재(섬유벨트 등)를 사용하여 작업을 진행하여야 함.
- 형태
- 충돌
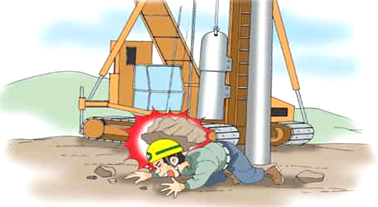
- 재해개요
- 강관파일 항타작업중 Auger를 인발 하면서 스크류 상부의 토사덩어리가 낙하하여 피재자 강타
- 재해원인
- 작업전 점검 및 조치 미흡
- 항타기 작업반경 내 접근금지 조치 미흡
- 안전대책
- Auger를 상승시키기 전 토사덩어리 낙하위험이 있을 시 제거후 작업 실시
- 항타기 작업반경내에는 근로자가 접근하지 못하도록 통제조치를 하여야 함
- 형태
- 낙하
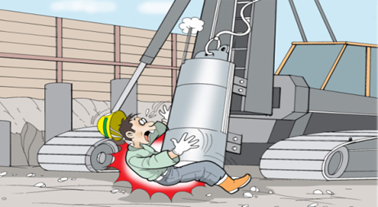
- 재해개요
- 파일 천공작업을 위해 항타장비를 후진하여 회전하던 중 항타기 해머(3ton)를 상부에서 지지하고 있던 와이어로프의 샤클이 풀리면서 해머가 낙하하여 피재자를 가격ㆍ사망
- 재해원인
- 항타기 해머 고정 미흡
- 항타기 작업 반경 내 접근금지 조치 미흡
- 안전대책
- 항타기의 권상용 와이어로프에 해머 등을 연결하는 때에는 탈락되지 않도록 클램프, 클립 등으로 견고하게 고정
- 항타작업반경 내에는 근로자가 접근하지 못하도록 출입통제를 철저히 하여야 함
- 형태
- 낙하
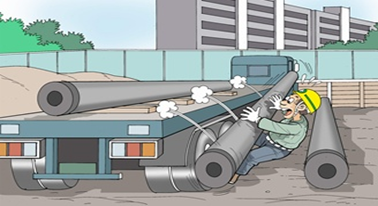
- 재해개요
- 트레일러(25ton)에 적재된 PHC파일을 지게차로 하역작업을 진행하던 중 피재자가 굴러 떨어지는 파일을 저지하려다 파일과 지면사이에 협착되어 사망한 재해
- 재해원인
- 구름방지용 쐐기설치 미흡
- 하역작업반경내 출입금지 조치 미흡
- 안전대책
- 구름방지용 쐐기를 견고히 설치토록 하여야 함.
- 하역작업 반경내에 기타 근로자가 출입하지 못하도록 통제를 철저히 하여야 함.
- 형태
- 협착
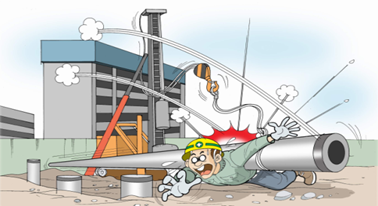
- 재해개요
- 항타기 근처에서 기초철근 조립작업을 진행하던 중, 항타기 운전원의 조작오류로 관입용 파일을 지지하고 있던 와이어로프 드럼이 역회전하여, 인양된 파일이 낙하 및 좌굴되어 피재자를 강타ㆍ사망한 재해
- 재해원인
- 안전장치 등 점검 미흡
- 항타기 작업반경 내 접근금지 조치 미흡
- 안전대책
- 항타기를 사용하는 때에는 권상기에 쐐기장치(Ratchet) 또는 역회전방지용 브레이크를 부착하여야 함.
- 천공ㆍ항타작업 반경내에는 작업 및 출입금지조치를 하여야 함.
- 형태
- 낙하
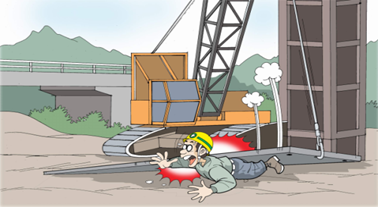
- 재해개요
- 항타기 전도방지용 철판에 연결된 후크를 제거하기 위해 대기하던 중, 지면에 내려놓으려던 철판에 협착되어 사망한 재해
- 재해원인
- 출입통제 조치 미흡
- 작업방법 불량
- 안전대책
- 항타기 등 차량계 건설기계를 사용하여 작업을 하는 때에는 근로자의 접촉으로 인한 충돌재해예방을 위해 출입통제를 취하거나 신호수를 두어 일정한 신호방법에 의해 작업이 진행되도록 하여야 함.
- 지반이 평탄한 작업장소에서는 항타기의 작업방식을 자동운전 조작방식으로 선정하여, 일정한 속도로 철판을 내려놓을 수 있도록 하여야 함.
- 형태
- 협착
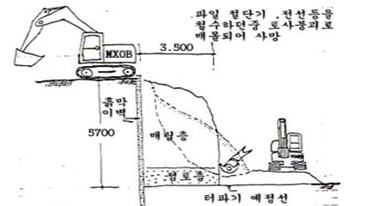
- 재해개요
- 터파기 작업장에서 파일 두부 정리작업과 터파기 고르기 작업을 하던 피재자가 작업을 마치고 전선, 공구 등을 철수하려던 중 굴착 법면이 붕괴되면서 매몰, 사망한 재해
- 재해원인
- 굴착법면 구배 미준수
- 굴착법면 하부에서의 작업에 대한 관리 감독 소홀
- 안전대책
- 굴착면의 구배 기준(보통흙 습지 1:1∼1:1.5 건지 1:0.5∼1:1) 상기 굴착면 구배를 유지하기 위해 BACK HOE를 굴착높이별 2단 배치 또는 상차용, 굴착용을 구분 배치등의 작업방법 개선
- 관리감독 및 근로자 안전교육 철저(굴착법면 하단부에 접근하여 작업을 금하도록 철저한 관리감독과 근로자 안전교육 철저)
- 형태
- 붕괴
반응형
'안전관리자 > 위험성 평가' 카테고리의 다른 글
터파기 작업 위험성 평가 (0) | 2024.05.30 |
---|---|
벌목 작업 위험성 평가 (0) | 2024.05.30 |
기초파일(PHC) 작업 위험성 평가 (0) | 2024.05.30 |
시스템동바리 설치 해체 작업 위험성 평가 (0) | 2024.05.30 |
가설방음벽 설치 작업 위험성 평가 (0) | 2024.05.30 |